Dodge the Bearing: A Comprehensive Guide to Avoiding Catastrophic Engine Failures
Introduction
Dodge bearings are essential components in internal combustion engines, responsible for reducing friction and wear between the crankshaft and connecting rods. However, bearing failures can lead to catastrophic engine damage, resulting in costly repairs and downtime. Understanding the causes and symptoms of bearing failures is crucial for preventing these costly issues.
Causes of Bearing Failures
-
Insufficient Lubrication: Inadequate or contaminated oil can starve bearings of the lubrication they need to function properly.
-
Excessive Load or Speed: Overloading the engine or operating at excessively high engine speeds can put undue stress on bearings, leading to premature failure.
-
Debris Ingestion: Foreign objects, such as metal shavings or dirt, can enter the engine through the oil system, causing damage to bearings.
-
Improper Installation: Incorrectly installed bearings can cause misalignment, leading to increased loads and premature failure.
-
Defective Bearings: Manufacturing defects or substandard materials can result in premature bearing failure.
Symptoms of Bearing Failures
-
Knocking or Ticking Noises: Loud knocking or ticking sounds from the engine can indicate bearing failure.
-
Oil Pressure Drop: A sudden drop in oil pressure is a sign of potential bearing problems.
-
Engine Overheating: Bearing failures can generate excessive heat, leading to engine overheating.
-
Metal Shavings in Oil: The presence of metal shavings in the engine oil is a clear indication of bearing damage.
-
Increased Engine Vibration: Severe bearing failures can cause excessive engine vibration, resulting in discomfort for operators.
Consequences of Bearing Failures
Bearing failures can have severe consequences, including:
-
Catastrophic Engine Damage: Complete engine failure, requiring a costly rebuild or replacement.
-
Downtime and Lost Productivity: Engine failures can result in significant downtime and lost productivity for businesses.
-
Increased Maintenance Costs: Repairing bearing failures can be expensive, and repeated failures can lead to increased maintenance costs.
-
Safety Hazards: Engine failures can pose safety hazards, especially in critical applications such as industrial machinery or commercial vehicles.
Preventing Bearing Failures
Preventing bearing failures requires a proactive approach, including:

-
Regular Maintenance: Regularly changing oil and filters and inspecting bearings for wear and damage is essential for preventing failures.
-
Proper Lubrication: Using the correct oil type and quantity for the specific engine is crucial for ensuring proper lubrication.
-
Avoid Overloading: Operating the engine within its specified load and speed limits is essential for preventing bearing damage.
-
Protect from Debris: Preventing foreign objects from entering the engine through the air intake or oil system is vital for avoiding bearing damage.
-
Proper Installation: Ensuring bearings are installed correctly, with the correct clearances and torque specifications, is critical for their proper function.
Troubleshooting Bearing Failures
Troubleshooting bearing failures involves:
-
Noise Tracing: Using a stethoscope or mechanic's ear can help pinpoint the location of bearing noises.
-
Oil Analysis: Examining the oil for metal shavings or excessive wear can provide insights into bearing health.
-
Engine Disassembly: In severe cases, disassembling the engine may be necessary to diagnose bearing failures accurately.
-
Bearing Inspection: Inspecting bearings for wear, damage, or misalignment can help determine the root cause of the failure.
-
Refer to Manufacturer's Recommendations: Consulting with the engine manufacturer or a qualified mechanic is essential for diagnosing and resolving bearing failures effectively.
Humorous Stories about Bearing Failures
-
The Case of the Mysterious Metal Shavings: A mechanic was puzzled by a persistent ticking noise in an engine. After disassembling the engine, he discovered a squirrel's nest in the oil pan, complete with metal shavings from the bearings chewed up by the furry culprit.
-
The Engine That Wouldn't Knock: A customer brought in a car for a knocking noise, but the mechanic couldn't reproduce the problem. Days later, the customer returned with the car loaded with passengers. As the mechanic started the car, the noise returned, prompting the owner to announce, "Oh, it only knocks when the family's all here!"
-
The Bearing That Went on Vacation: A truck driver ignored his mechanic's advice to replace worn bearings promptly. As a result, a bearing failed on a remote highway, stranding him in the wilderness with all his worldly belongings piled up in the trailer.
Lesson Learned: Ignoring bearing issues can lead to unexpected and potentially costly consequences.
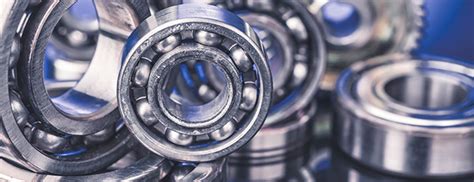
Tables on Bearing-Related Data
Table 1: Common Bearing Failure Modes
Failure Mode |
Description |
Causes |
Spalling |
Surface pitting and flaking |
Lubrication starvation, excessive load |
Scuffing |
Metal-to-metal contact and scoring |
Inadequate lubrication, overheating |
Wear |
Gradual material loss |
Abrasive debris, misalignment |
Fatigue |
Crack formation and propagation |
Cyclic loading, high stresses |
Seizure |
Sudden locking of bearing |
Lack of lubrication, overheating |
Table 2: Bearing Life Expectancy by Lubrication Type
Lubrication Type |
Life Expectancy |
Plain Bearings (no lubrication) |
500 hours |
Sleeve Bearings (oil bath) |
5,000 hours |
Ball Bearings (grease) |
50,000 hours |
Roller Bearings (oil bath) |
100,000 hours |
Table 3: Bearing Load Capacity by Type
Bearing Type |
Load Capacity (lbs) |
Plain Bearings |
500 |
Sleeve Bearings |
1,000 |
Ball Bearings |
5,000 |
Roller Bearings |
10,000 |
Tips and Tricks for Handling Bearings
- Store bearings in a clean, dry environment to prevent contamination.
- Use a bearing puller to remove bearings safely and avoid damage.
- Inspect bearings before installation for any signs of damage or wear.
- Ensure proper bearing clearance by measuring the bearing journal and using the appropriate spacers or shims.
- Lubricate bearings with the correct type and amount of lubricant before installation.
- Run the engine at low speed for a short period (break-in period) after installing new bearings to allow them to settle in.
Common Mistakes to Avoid
- Do not hammer or chisel bearings into place, as this can damage them.
- Do not over-tighten bearing bolts or nuts, as this can create excessive friction and premature wear.
- Do not use bearings that have been subjected to extreme heat or cold, as they may have lost their strength or accuracy.
- Do not mix bearings from different manufacturers or models, as they may not be compatible.
- Do not ignore bearing noises or other signs of potential failure, as they can lead to catastrophic damage.
Call to Action
Dodge bearing failures by following these guidelines and tips. Regular maintenance, proper lubrication, and prompt attention to warning signs can help prevent costly repairs and downtime. By understanding the causes, symptoms, and consequences of bearing failures, you can ensure the longevity and reliability of your engines. Remember, dodge the bearing and protect your equipment from catastrophic damage.