Unlock the Power of Smooth Performance: A Comprehensive Guide to Installing Buddy Bearings
Introduction
In the realm of mechanical systems, buddy bearings play a crucial role in ensuring smooth operation and extended component life. These precision-engineered bearings work in tandem to accommodate axial and radial loads, minimizing friction and preventing premature wear. Installing buddy bearings is a critical task that requires a combination of knowledge, skill, and attention to detail. This comprehensive guide will provide you with step-by-step instructions, helpful tips, and essential considerations for a successful installation. Embrace the power of buddy bearings and elevate the performance of your mechanical systems to new heights.
Understanding Buddy Bearings
Buddy bearings, also known as duplex bearings, consist of two identical bearings that are mounted back-to-back in a single housing. This unique arrangement allows for the distribution of loads across both bearings, reducing stress and prolonging lifespan. Buddy bearings are commonly used in applications that demand high precision, such as machine tools, pumps, and turbines.
Advantages of Buddy Bearings
-
Increased Load Capacity: Buddy bearings can accommodate significantly higher radial and axial loads compared to single bearings due to their double row design.
-
Improved Rigidity: The back-to-back mounting provides increased rigidity, reducing shaft deflection and maintaining alignment accuracy.
-
Reduced Friction: The precision fit and optimized geometry of buddy bearings minimize friction, resulting in smoother operation and reduced power consumption.
-
Extended Component Life: The reduced stress and friction experienced by buddy bearings lead to extended component life and reduced maintenance intervals.
Types of Buddy Bearings
Buddy bearings are available in various types, each designed for specific applications. The most common types include:

-
Angular Contact Buddy Bearings: Designed to accommodate axial and radial loads simultaneously, ideal for high-speed applications.
-
Cylindrical Roller Buddy Bearings: Suitable for heavy radial loads, providing excellent stability and rigidity.
-
Tapered Roller Buddy Bearings: Designed for combined radial and thrust loads, often used in automotive and industrial machinery.
Selecting the Right Buddy Bearings
Choosing the appropriate buddy bearings for your application requires careful consideration of the following factors:
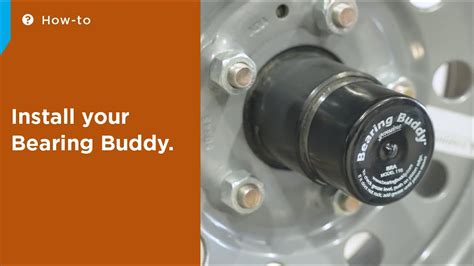
-
Load Capacity: Determine the expected radial and axial loads that the bearings will encounter.
-
Speed: Consider the operating speed of the shaft to ensure the bearings are suitable for the application.
-
Lubrication: Select bearings that are compatible with the available lubrication system and environmental conditions.
-
Clearance: Choose bearings with appropriate internal clearance to accommodate thermal expansion and misalignment.
-
Housing: Ensure that the bearing housing is properly designed to withstand the loads and provide adequate support.
Step-by-Step Installation Guide
-
Prepare the Housing: Clean and inspect the bearing housing, ensuring that it is free from debris and damage.
-
Mount the Bearings: Carefully insert the buddy bearings into the housing, ensuring that they are aligned properly.
-
Apply Lubricant: Lubricate the bearings according to the manufacturer's specifications to minimize friction and extend their life.
-
Install the Shaft: Carefully insert the shaft into the bearings, ensuring that it is centered and aligned.
-
Adjust Preload: Adjust the preload on the bearings using the manufacturer's recommended method to achieve the desired operating clearance.
-
Install Seals: If required, install appropriate seals to prevent contamination and lubricant leakage.
-
Tighten Components: Tighten all housing components securely, ensuring proper bearing alignment and preventing movement.
-
Inspect and Test: Inspect the installation thoroughly and perform a test run to ensure smooth operation and absence of excessive noise or vibration.
Tips and Tricks
-
Use Specialized Tools: Invest in specialized tools designed for bearing installation to ensure precision and accuracy.
-
Maintain Cleanliness: Keep the work area and components clean to prevent contamination.
-
Follow Manufacturer's Instructions: Adhere strictly to the manufacturer's installation guidelines to ensure optimal performance and longevity.
-
Monitor Regularly: Regularly monitor the performance of buddy bearings to detect any signs of wear or misalignment.
-
Consider Professional Installation: If you lack experience or confidence, consider seeking professional assistance for bearing installation.
Pros and Cons of Buddy Bearings
Pros:
- Increased load capacity
- Improved rigidity
- Reduced friction
- Extended component life
Cons:

- Higher initial cost compared to single bearings
- More complex installation process
- May require specialized housing design
Call to Action
Unlock the full potential of your mechanical systems by embracing the power of buddy bearings. By following the guidelines outlined in this comprehensive guide, you can ensure a successful installation, optimizing performance, and maximizing the lifespan of your components. Invest in quality buddy bearings and experience the difference they make in the smooth and efficient operation of your machinery.
Three Humorous Stories About Buddy Bearings
-
The Stubborn Mechanic: Sam, a mechanic known for his meticulous nature, struggled for hours to install buddy bearings on a complex machine. After finally completing the task, he realized he had installed them backward.
Lesson Learned: Always double-check your installation before tightening everything down.
-
The Grease Monkey: Mark, an overzealous grease enthusiast, applied an excessive amount of lubricant to his buddy bearings. The result? A grease-soaked mess that attracted dirt and caused premature bearing failure.
Lesson Learned: Avoid over-lubrication as it can attract contaminants and reduce bearing performance.
-
The Noisy Neighbor: Bob's washing machine started making a racket that could be heard throughout the neighborhood. Upon inspection, he discovered that one of the buddy bearings had become misaligned and was rubbing against the housing.
Lesson Learned: Regular monitoring of buddy bearings can help detect potential problems before they cause major breakdowns.
Authoritative Website
SKF
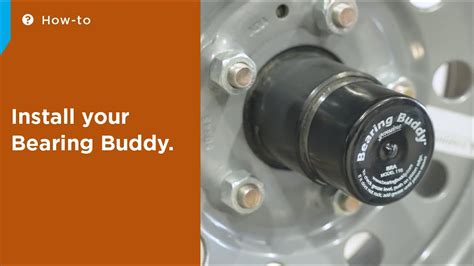
Tables
Table 1: Buddy Bearing Types and Applications
Bearing Type |
Applications |
Angular Contact |
High-speed applications, axial and radial loads |
Cylindrical Roller |
Heavy radial loads, stable and rigid |
Tapered Roller |
Combined radial and thrust loads, automotive and industrial machinery |
Table 2: Buddy Bearing Selection Criteria
Selection Criteria |
Considerations |
Load Capacity |
Radial and axial loads |
Speed |
Operating speed of the shaft |
Lubrication |
Compatibility with available lubrication system |
Clearance |
Thermal expansion and misalignment |
Housing |
Design suitability and support |
Table 3: Buddy Bearing Installation Sequence
Step |
Action |
1 |
Prepare the housing |
2 |
Mount the bearings |
3 |
Apply lubricant |
4 |
Install the shaft |
5 |
Adjust preload |
6 |
Install seals |
7 |
Tighten components |
8 |
Inspect and test |