Unveiling the Intricacies of Bandsaw Guide Bearings: A Comprehensive Guide
Introduction
Bandsaw guide bearings play a crucial role in the smooth and precise operation of bandsaws. These bearings support the bandsaw blade, ensuring its stability and alignment as it cuts through various materials. In this comprehensive guide, we will delve into the intricacies of bandsaw guide bearings, exploring their functions, types, selection criteria, maintenance practices, and various aspects that contribute to their effectiveness.
Functions of Bandsaw Guide Bearings
-
Blade Support: Guide bearings provide support to the bandsaw blade, preventing it from wobbling or twisting during operation.
-
Blade Alignment: They maintain the blade's alignment, ensuring accurate cuts and minimizing deviations.
-
Friction Reduction: Guide bearings reduce friction between the blade and the saw table, allowing for smooth and efficient cutting.
-
Stability Enhancement: By supporting the blade and maintaining its alignment, guide bearings contribute to the overall stability of the bandsaw, reducing vibrations and ensuring precise cuts.
Types of Bandsaw Guide Bearings
Bandsaw guide bearings come in various types, each designed to meet specific requirements:
-
Ball Bearings: These bearings utilize small, spherical balls to facilitate smooth blade movement.
-
Roller Bearings: Roller bearings employ cylindrical rollers for reduced friction and higher load capacity.
-
Needle Bearings: Needle bearings are compact and have a long, thin shape, making them suitable for limited space applications.
-
Ceramic Bearings: Ceramic bearings provide exceptional durability, corrosion resistance, and heat tolerance.
-
Sealed Bearings: Sealed bearings protect against contamination and require less frequent maintenance.
Selecting the Right Bandsaw Guide Bearings
Choosing the appropriate bandsaw guide bearings depends on several factors:
-
Blade Size and Type: The size and type of the bandsaw blade will determine the required bearing size and capacity.
-
Material Compatibility: Bearings should be compatible with the bandsaw blade's material to avoid premature wear or damage.
-
Operating Conditions: Factors such as speed, load, and duty cycle should be considered when selecting bearings for demanding applications.
-
Maintenance Requirements: Some bearings require regular lubrication or replacement, while others are designed for low-maintenance operation.
Maintenance of Bandsaw Guide Bearings
Proper maintenance of bandsaw guide bearings is essential for their longevity and performance:

-
Regular Cleaning: Remove dust and debris from bearings to prevent abrasive wear and premature failure.
-
Lubrication: Follow manufacturer's instructions for lubrication frequency and type. Proper lubrication reduces friction and extends bearing life.
-
Replacement: Worn or damaged bearings must be replaced to maintain optimal performance and prevent further issues.
Why Bandsaw Guide Bearings Matter
High-quality bandsaw guide bearings offer numerous advantages:
-
Increased Precision: Proper bearing support ensures precise cuts, minimizing deviation and waste.
-
Enhanced Efficiency: Reduced friction and smooth blade movement allow for more efficient cutting, saving time and energy.
-
Longer Blade Life: Properly maintained bearings support the blade, reducing blade wear and prolonging its lifespan.
-
Reduced Maintenance Costs: Preventive maintenance and the use of durable bearings can minimize costly repairs and downtime.
Benefits of High-Quality Bandsaw Guide Bearings
Investing in high-quality bandsaw guide bearings provides several tangible benefits:
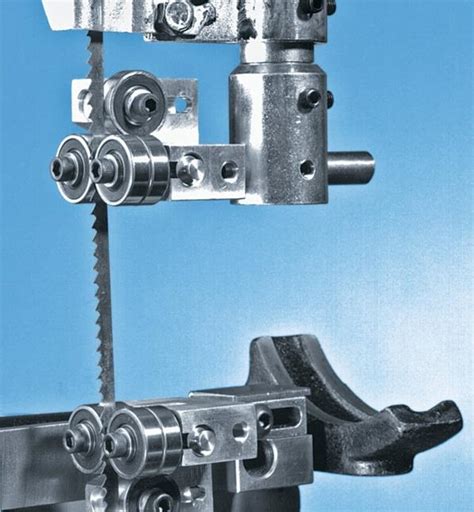
-
Improved Cut Quality: Precision bearings ensure accurate and clean cuts, enhancing the overall quality of the finished product.
-
Increased Productivity: Efficient bearings reduce cutting time, leading to increased productivity and output.
-
Reduced Operating Costs: Durable bearings minimize maintenance costs and downtime, lowering overall operating expenses.
-
Enhanced Safety: Properly supported blades reduce the risk of accidents and injuries, creating a safer work environment.
Common Mistakes to Avoid
To ensure optimal performance and longevity of bandsaw guide bearings, avoid these common mistakes:

-
Overtightening: Excessive tightening of bearings can cause premature wear and failure.
-
Undertightening: Loose bearings can lead to vibration, misalignment, and reduced blade life.
-
Incorrect Lubrication: Using the wrong type or insufficient lubrication can damage bearings and shorten their lifespan.
-
Ignoring Warning Signs: Neglecting unusual noises or vibrations can indicate bearing issues that require attention.
-
Improper Installation: Incorrect installation can compromise bearing performance and lead to premature failure.
Effective Strategies for Maintaining Bandsaw Guide Bearings
Implement these effective strategies to maximize the lifespan and performance of bandsaw guide bearings:
-
Establish a Regular Maintenance Schedule: Implement a routine maintenance plan that includes regular cleaning, lubrication, and inspection.
-
Use High-Quality Bearings: Invest in durable and reliable bearings designed for bandsaw applications.
-
Lubricate Properly: Follow manufacturer's guidelines for lubrication frequency and type to ensure optimal bearing performance.
-
Monitor Bearing Condition: Regularly inspect bearings for signs of wear, damage, or misalignment.
-
Train Operators: Provide proper training to operators on bearing maintenance and troubleshooting to prevent misuse and premature failure.
Humorous Stories to Remember
-
The Wobbly Woodsman: A woodworker neglected to replace worn guide bearings, resulting in a wobbly blade that produced comical, crooked cuts.
-
The Screaming Saw: A technician used the wrong lubricant on guide bearings, leading to a piercing screech that echoed through the workshop, earning the bandsaw the nickname "The Screaming Saw."
-
The Blade Bender: An inexperienced operator tightened the guide bearings excessively, causing the bandsaw blade to bend and snap, narrowly missing the operator's fingers.
Maintenance Task |
Frequency |
Benefits |
Cleaning |
Daily |
Removes dust and debris, preventing premature wear |
Lubrication |
Weekly |
Reduces friction, extends bearing life |
Inspection |
Monthly |
Identifies potential issues early on, preventing catastrophic failure |
Replacement |
As needed |
Ensures optimal performance, prevents damage to blade and other components |
Bearing Type |
Applications |
Advantages |
Disadvantages |
Ball Bearings |
General-purpose applications |
Low cost, easy installation |
Limited load capacity, higher friction |
Roller Bearings |
High-load applications |
High load capacity, reduced friction |
More expensive, more complex installation |
Needle Bearings |
Space-constrained applications |
Compact, high load capacity |
Sensitive to contamination, require specialized lubrication |
Ceramic Bearings |
High-speed, high-heat applications |
Exceptional durability, corrosion resistance |
More expensive, more fragile |
Maintenance Procedure |
Step-by-Step Instructions |
Safety Precautions |
Bearing Cleaning |
|
|
- Remove blade and guide assembly |
|
|
- Use compressed air or soft brush to remove debris |
|
|
- Inspect bearings for visible damage |
|
|
Wear appropriate safety gear, including gloves and eye protection. |
|
|
Bearing Lubrication |
|
|
- Apply a thin, even layer of lubricant to bearings |
|
|
- Rotate bearings by hand to distribute lubricant |
|
|
- Avoid over-lubricating |
|
|
Use only lubricants specifically designed for bandsaw guide bearings. |
|
|
Bearing Inspection |
|
|
- Look for signs of wear, damage, or misalignment |
|
|
- Listen for unusual noises or vibrations |
|
|
- Check bearing tightness |
|
|
Disconnect power to bandsaw before performing any maintenance. |
|
|