Unraveling the World of AMI Bearings: A Comprehensive Guide to Types, Applications, Maintenance, and Benefits
AMI bearings, a cornerstone of countless industries, play a pivotal role in enabling seamless motion, reducing friction, and enhancing efficiency across a vast array of applications. This comprehensive guide delves into the intricate world of AMI bearings, exploring their diverse types, exploring their diverse types, examining their wide-ranging applications, providing expert maintenance tips, and highlighting their myriad benefits.
Types of AMI Bearings
AMI bearings encompass a vast array of types, each tailored to specific performance requirements and applications. The most common types include:
-
Ball bearings: The most prevalent type, characterized by their simple design, low friction, and high speed capabilities.
-
Roller bearings: Known for their ruggedness, high load capacity, and ability to withstand heavy axial loads.
-
Needle bearings: Ultra-thin bearings with a high load capacity relative to their size, ideal for applications with limited space.
-
Thrust bearings: Designed to handle axial loads, typically used in pumps, compressors, and gearboxes.
Applications of AMI Bearings
AMI bearings find widespread application across a multitude of industries, including:
-
Automotive: Transmissions, engines, pumps, and suspension systems.
-
Aerospace: Landing gear, control systems, and engines.
-
Industrial: Pumps, conveyors, turbines, and gearboxes.
-
Medical: Surgical instruments, imaging equipment, and prosthetics.
-
Electronics: Hard drives, printers, and scanners.
Maintenance of AMI Bearings
Ensuring optimal performance and longevity of AMI bearings requires proper maintenance practices. Key guidelines include:

-
Regular lubrication: Using the correct type and amount of lubricant is crucial to minimize friction and wear.
-
Monitoring temperature: Excessive heat can damage bearings; regular temperature checks help detect potential issues.
-
Cleaning: Removing contaminants such as dirt, moisture, and debris prevents premature bearing failure.
-
Inspection: Visual and ultrasonic inspections can identify potential problems before they become critical.
Benefits of AMI Bearings
Incorporating AMI bearings into machinery and equipment offers numerous advantages:
-
Reduced friction: AMI bearings minimize friction, leading to energy savings and improved efficiency.
-
Enhanced load capacity: Certain types of AMI bearings, such as roller bearings, can handle substantial loads.
-
Increased precision: Precision bearings enable smooth and accurate motion, essential for many applications.
-
Extended lifespan: Proper maintenance can significantly extend the lifespan of AMI bearings, reducing maintenance costs.
-
Reduced noise and vibration: AMI bearings operate with minimal noise and vibration, improving work environments.
Comparison of Pros and Cons
Pros:
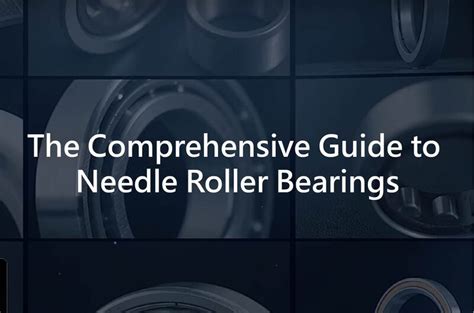

- Low friction and high efficiency
- Wide range of types and sizes
- Relatively low maintenance requirements
- Long lifespan with proper care
Cons:
- Can be expensive
- Sensitive to misalignment or excessive loads
- May require specialized knowledge for optimal maintenance
Frequently Asked Questions (FAQs)
-
What is the difference between a ball bearing and a roller bearing?
Ball bearings use rolling balls, while roller bearings use cylindrical rollers; roller bearings typically have a higher load capacity.
-
How often should I lubricate my AMI bearings?
Lubrication frequency depends on the bearing type, operating conditions, and manufacturer recommendations.
-
What are the signs of a failing AMI bearing?
Excessive noise, vibration, heat, and decreased efficiency are common indicators of bearing failure.
-
Can AMI bearings be repaired?
Minor repairs may be possible for certain types of bearings, but replacement is usually recommended.
-
How do I choose the right AMI bearing for my application?
Factors to consider include bearing type, load capacity, speed requirements, and environmental conditions.
-
Where can I find reputable AMI bearing manufacturers?
Numerous reputable manufacturers exist; research and compare their products and services before purchasing.
Humorous Stories and Lessons Learned
-
The Case of the Rolling Thunder:
A factory's conveyor system repeatedly malfunctioned due to excessive noise and vibration. Investigation revealed a misaligned roller bearing; once corrected, the system operated smoothly and quietly, earning the nickname "Rolling Thunder." Lesson: Misalignment can have serious consequences for bearing performance.
-
The Greasy Dip:
A technician accidentally over-lubricated a ball bearing, causing it to leak grease onto a nearby electrical panel. The resulting short circuit shut down the entire production line for hours. Lesson: Follow lubrication instructions carefully to avoid costly mistakes.
-
The Bearing Bonehead:
A construction worker accidentally dropped a heavy beam on a precision ball bearing, shattering it. The project was delayed significantly while waiting for a replacement bearing. Lesson: Handle bearings with care to prevent costly accidents.
Effective Strategies for Optimizing AMI Bearing Performance
-
Use the right bearing for the job: Choose the bearing type and size that best meets the specific application requirements.
-
Lubricate properly: Follow manufacturer recommendations for lubrication type and frequency to minimize friction and wear.
-
Inspect regularly: Schedule periodic inspections to identify potential issues before they become critical.
-
Monitor temperature and vibration: Excessive heat or vibration can indicate bearing problems.
-
Store and handle properly: Store bearings in a clean, dry environment and handle them with care to prevent damage.
-
Seek professional assistance: Consult with experts in bearing selection and maintenance for optimal results.
Why AMI Bearings Matter
AMI bearings play a crucial role in the smooth and efficient operation of countless machines and equipment across various industries. Their ability to reduce friction, handle loads, and enhance precision is essential for achieving optimal performance, reliability, and longevity in a wide range of applications. By understanding the types, applications, maintenance practices, and benefits of AMI bearings, engineers and technicians can make informed decisions to maximize the performance and lifespan of their equipment.
Call to Action
Incorporating AMI bearings into your machinery and equipment can significantly enhance performance, efficiency, and lifespan. By following the best practices outlined in this comprehensive guide, you can maximize the benefits of AMI bearings and drive success in your industry. Contact reputable bearing manufacturers today to explore the wide range of AMI bearings available and find the ideal solution for your specific needs.
Bearing Type |
Advantages |
Disadvantages |
Ball Bearings |
Low friction and high speed, low noise |
Lower load capacity |
Roller Bearings |
High load capacity and durability, shock resistance |
Higher friction and noise |
Needle Bearings |
Compact and high load capacity, lightweight |
Lower speed capabilities |
Thrust Bearings |
Handles axial loads, low friction |
Lower load capacity |
Hybrid Bearings |
Combine advantages of different bearing types, high performance |
More expensive |
Application |
Bearing Types |
Benefits |
Automotive Transmissions |
Ball Bearings, Roller Bearings |
Reduced friction, increased efficiency |
Aerospace Landing Gear |
Roller Bearings, Thrust Bearings |
High load capacity, shock resistance |
Industrial Pumps |
Ball Bearings, Roller Bearings |
Reliability, durability |
Medical Surgical Instruments |
Precision Ball Bearings |
Accuracy, precision |
Electronics Printers |
Ball Bearings, Needle Bearings |
Low noise, low friction |
Maintenance Task |
Importance |
Frequency |
Lubrication |
Reduces friction and wear |
As per manufacturer recommendations |
Temperature Monitoring |
Detects potential problems |
Regular checks |
Cleaning |
Removes contaminants |
As needed |
Inspection |
Identifies potential issues |
Visual and ultrasonic inspections |
Replacement |
Prevents catastrophic failure |
As per bearing lifespan and operating conditions |