Thrust Washers: An Essential Guide to Maintaining Shaft Alignment and Preventing Friction
Thrust washers are crucial components in machinery, playing a pivotal role in maintaining shaft alignment, reducing friction, and extending equipment lifespan. This comprehensive guide delves into the intricacies of thrust washers, their types, applications, and best practices for their maintenance and replacement.
What Are Thrust Washers?
Thrust washers are thin, disc-shaped components that are placed between two rotating or sliding surfaces to prevent direct contact and reduce friction. Their primary function is to bear axial loads, or thrust forces, that are perpendicular to the shaft's axis of rotation.
Types of Thrust Washers
Thrust washers come in various types, each designed for specific applications and load requirements:
-
Flat Thrust Washers: These are simple washers with flat surfaces on both sides. They are suitable for low-load applications.
-
Spherical Thrust Washers: They have a concave surface on one side and a convex surface on the other. This design allows for minor misalignments and accommodates axial and radial loads.
-
Tapered Thrust Washers: These have a tapered bore that matches the shaft's taper. They are effective in high-speed applications and can handle significant thrust loads.
-
Belleville Thrust Washers: Also known as disc springs, these have a washer-like shape but have a curved profile. They provide a progressive spring force and are used in applications where space is limited.
Applications of Thrust Washers
Thrust washers find widespread applications in various industries, including:
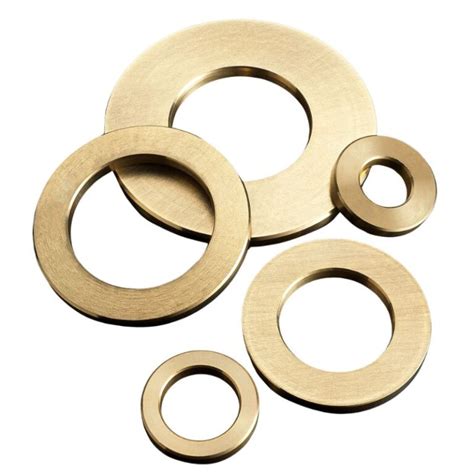
- Automotive: Transmission systems, differentials, and engine components
- Aerospace: Aircraft engines, landing gear, and flight control systems
- Industrial machinery: Compressors, pumps, and gearboxes
- Medical devices: Surgical instruments and prosthetic joints
Materials Used for Thrust Washers
Thrust washers are typically made of durable materials that can withstand friction, wear, and harsh operating conditions. Common materials include:
-
Steel: Provides high strength and durability.
-
Bronze: Offers good wear resistance and corrosion resistance.
-
PTFE (Teflon): Has low friction and is suitable for high-temperature applications.
-
Carbon Graphite: Exhibits self-lubricating properties and is used in high-pressure environments.
Benefits of Using Thrust Washers
Installing thrust washers offers numerous benefits for machinery operations:

-
Reduced Friction: They minimize direct contact between moving surfaces, reducing friction and wear.
-
Extended Equipment Lifespan: By reducing friction and wear, thrust washers extend the lifespan of shafts, bearings, and other components.
-
Improved Shaft Alignment: They help maintain proper shaft alignment, reducing vibration and noise levels.
-
Increased Load Capacity: Thrust washers can handle high axial loads, allowing for increased load-bearing capacity.
Best Practices for Maintenance and Replacement
To ensure optimal performance and longevity of thrust washers, proper maintenance and replacement are essential:
Maintenance
-
Regular Inspection: Regularly inspect thrust washers for signs of wear, damage, or misalignment.
-
Lubrication: Apply appropriate lubrication to reduce friction and prevent premature wear.
-
Cleanliness: Keep thrust washers clean and free of contamination to prevent damage and ensure proper operation.
Replacement
-
Indications of Replacement: Replace thrust washers when they show excessive wear, damage, or misalignment.
-
Proper Installation: Ensure proper installation of new thrust washers, following manufacturer guidelines.
-
Tightening Torque: Apply the correct tightening torque to the thrust washer assembly to prevent over-tightening or loosening.
Step-by-Step Approach to Thrust Washer Replacement
-
Safety First: Wear appropriate safety gear and observe all safety precautions.
-
Disassembly: Disassemble the machinery component(s) to access the thrust washer.
-
Inspection: Inspect the old thrust washer for signs of wear or damage.
-
Measurement: Measure the dimensions of the old thrust washer to determine the replacement size.
-
Cleaning: Clean the seating surfaces where the thrust washer will be installed.
-
Installation: Install the new thrust washer, ensuring proper alignment and orientation.
-
Tightening: Tighten the thrust washer assembly to the specified torque.
-
Reassembly: Reassemble the machinery component(s).
-
Testing: Test the machinery to verify proper operation.
Commonly Asked Questions
1. What is the difference between a thrust washer and a bearing?

Thrust washers bear axial loads while bearings bear radial loads.
2. What causes premature failure of thrust washers?
Overloading, misalignment, improper lubrication, and contamination can lead to premature failure.
3. How often should thrust washers be inspected?

Inspection frequency depends on the application and operating conditions; regular inspection is recommended.
Conclusion
Thrust washers are indispensable components in machinery, enabling efficient operation and reducing wear and tear. By understanding their types, applications, and best practices for maintenance and replacement, engineers and technicians can ensure optimal performance and longevity of their equipment. Regular monitoring, preventive maintenance, and prompt replacement of worn-out thrust washers will contribute to increased machine reliability, reduced downtime, and enhanced safety.