Thrust Washers: A Comprehensive Guide for Smooth Operation
Introduction
Thrust washers are crucial components in mechanical systems, responsible for transmitting axial thrust loads while minimizing friction. This article provides a comprehensive guide to thrust washers, discussing their types, materials, applications, and best practices for optimal performance.
Types of Thrust Washers
Thrust washers come in various types, each designed for specific applications:
-
Flat Washers: Plain washers with a uniform thickness, used for general-purpose applications with low axial loads.
-
Tapered Washers: Washers with a tapered face, providing self-alignment and compensating for misalignment between mating surfaces.
-
Belleville Washers: Conical-shaped washers that exhibit a high spring rate, suitable for applications requiring high thrust loads.
-
Spherical Washers: Curved washers that accommodate angular misalignment and high axial loads.
Materials for Thrust Washers
The material selection for thrust washers is critical and depends on factors such as load, friction, wear resistance, and operating environment. Common materials include:
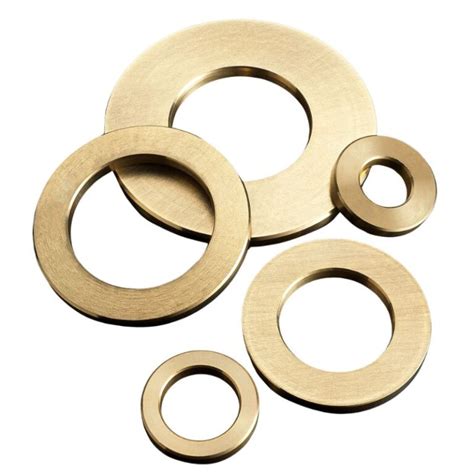
-
Steel: Durable and wear-resistant, suitable for high-load applications.
-
Bronze: Offers low friction and good corrosion resistance, used in precision instruments and marine environments.
-
Polymer: Lightweight and self-lubricating, suitable for low-to-medium load applications.
-
Ceramic: Highly wear-resistant and thermally stable, used in extreme conditions.
Applications of Thrust Washers
Thrust washers find applications in various industries, including:
-
Automotive: Transmissions, differentials, and engines
-
Industrial Machinery: Bearings, pumps, and motors
-
Aerospace: Landing gear, actuators, and control systems
-
Medical Equipment: Surgical instruments and prosthetics
Tips for Optimal Performance
To ensure optimal performance of thrust washers, follow these tips:
-
Proper Sizing: Select washers with the correct dimensions to match the load and surface area requirements.
-
Surface Finish: Ensure smooth surface finishes to minimize friction and prevent wear.
-
Lubrication: Use appropriate lubricants to reduce friction and extend washer life.
-
Alignment: Ensure proper alignment of mating surfaces to prevent uneven wear and premature failure.
-
Inspection: Regularly inspect thrust washers for signs of wear, damage, or misalignment.
Common Mistakes to Avoid
Avoid the following common mistakes to prevent premature failure of thrust washers:
-
Overloading: Exceeding the load capacity of the washer can lead to catastrophic failure.
-
Insufficient Lubrication: Inadequate lubrication causes excessive friction, heat buildup, and wear.
-
Misalignment: Incorrect alignment stresses the washer, reduces its load-bearing capacity, and promotes uneven wear.
-
Improper Installation: Tightening washers too much or using incorrect assembly methods can compromise their performance.
Advantages and Disadvantages of Using Thrust Washers
Advantages:

- Reduced friction for smoother operation
- Axial load transmission for improved performance
- Wear resistance for extended service life
- Self-alignment capabilities for misalignment compensation
Disadvantages:
- Potential for noise generation in certain applications
- Contact stress if load capacity is exceeded
- Limited radial load-bearing capability
Effective Strategies for Thrust Washer Applications
-
Use Preloaded Thrust Washers: Preloading washers reduces axial play and improves load distribution.
-
Consider Thrust Washers with Integral Seals: This eliminates the need for separate sealing components.
-
Optimize Washer Design: Choose the appropriate type, material, and dimensions to maximize performance.
-
Implement Effective Lubrication Practices: Use appropriate lubricants and lubrication schedules to extend washer life.
Troubleshooting Thrust Washer Problems
Common problems with thrust washers include:
-
Wear: Inspect washers for signs of wear and replace as necessary.
-
Misalignment: Check the alignment of mating surfaces and correct any misalignment.
-
Noise: Reduce noise by using thrust washers with a low coefficient of friction or by applying damping materials.
-
Premature Failure: Determine the root cause of premature failure (e.g., overloading, lubrication issues, misalignment) and address it.
Conclusion
Thrust washers are essential components for transmitting axial loads in mechanical systems. By understanding their types, materials, applications, and best practices, you can ensure optimal performance and extend the life of your machinery.