Thrust Washers: A Comprehensive Guide
Introduction
Thrust washers are critical components in various mechanical systems, primarily designed to transmit axial thrust loads while preventing relative motion between mating surfaces. Understanding the functions, types, materials, and applications of thrust washers is essential for engineers and designers seeking optimal performance and reliability in their mechanical systems.
Types of Thrust Washers
Thrust washers come in diverse designs to meet specific application requirements:
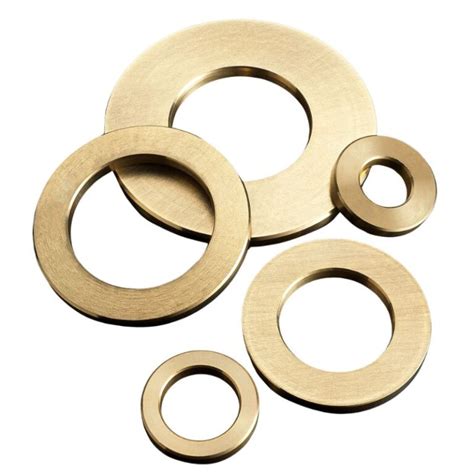
-
Flat Thrust Washers: Simple, thin discs used for low-load applications.
-
Tapered Thrust Washers: Tapered design provides higher load capacity for a given axial thickness.
-
Collared Thrust Washers: Feature a collar that prevents axial displacement.
-
Inlaid Thrust Washers: Bi-metallic thrust washers with a harder outer layer for improved wear resistance.
-
Preloaded Thrust Washers: Pre-loaded springs ensure constant contact and minimize axial movement.
-
Needle Thrust Washers: Incorporate needle bearings for reduced friction and higher load capacity.
Materials for Thrust Washers
The material selection for thrust washers depends on the operating conditions and required performance:
-
Steel: Common for moderate loads and general-purpose applications.
-
Bronze: Excellent wear resistance and conforms to mating surfaces.
-
Aluminum: Lightweight and corrosion-resistant option for low-load applications.
-
Babbitt: Soft metal alloy for high-load, low-speed applications.
-
Composite Materials: Offer high strength-to-weight ratio and reduced friction.
Applications of Thrust Washers
Thrust washers play a crucial role in a wide range of industries:
-
Automotive: Transmissions, differentials, and steering systems.
-
Industrial Machinery: Pumps, compressors, and gearboxes.
-
Aerospace: Engines, landing gear, and flight control systems.
-
Construction Equipment: Cranes, excavators, and forklifts.
-
Medical Devices: Orthopedic implants and surgical instruments.
Design Considerations for Thrust Washers
-
Load Capacity: Determine the maximum axial thrust load to select an appropriate washer thickness and material.
-
Speed: Consider the operating speed to prevent excessive heat generation and wear.
-
Lubrication: Ensure proper lubrication to minimize friction and improve performance.
-
Surface Finish: Fine surface finishes reduce friction and enhance load capacity.
-
Axial Clearance: Allow for sufficient axial clearance to prevent binding or damage.
Common Mistakes to Avoid
-
Undersizing: Selecting a thrust washer with insufficient load capacity can lead to premature failure.
-
Oversizing: Unnecessary thickness increases cost and may not improve performance.
-
Improper Material Selection: Using unsuitable materials can result in excessive wear or reduced lifespan.
-
Poor Surface Finish: Rough surfaces increase friction and reduce load capacity.
-
Insufficient Clearance: Inadequate axial clearance can cause binding or damage.
Pros and Cons
Advantages:
- Transmit axial thrust loads effectively.
- Prevent relative motion between mating surfaces.
- Minimize friction and wear.
- Extend component lifespan.
- Improve system reliability.
Disadvantages:
- Can add cost and complexity to systems.
- May require lubrication in certain applications.
- Thick washers can increase axial space requirements.
Conclusion
Trust washers are essential components that play a vital role in the performance and functionality of mechanical systems. By choosing the right type, material, and design considerations, engineers and designers can optimize the effectiveness and lifespan of their systems. Avoiding common mistakes and understanding the pros and cons of thrust washers ensures reliable and efficient operation.

Additional Information
Table 1: Thrust Washer Load Capacities (Steel)

Material |
Washer Thickness |
Load Capacity (N) |
AISI 1010 |
0.5 mm |
6,000 |
AISI 1020 |
1.0 mm |
12,000 |
AISI 4140 |
1.5 mm |
18,000 |
Table 2: Coefficients of Friction for Thrust Washer Materials
Material |
Coefficient of Friction |
Steel |
0.15-0.25 |
Bronze |
0.05-0.15 |
Aluminum |
0.10-0.20 |
Babbitt |
0.01-0.05 |
Table 3: Thermal Conductivity of Thrust Washer Materials
Material |
Thermal Conductivity (W/m-K) |
Steel |
50 |
Bronze |
85 |
Aluminum |
230 |
Babbitt |
40 |
Stories and Lessons Learned
-
Story 1: A manufacturing plant experienced premature failure of thrust washers in its gearboxes. Analysis revealed that the washers were undersized and made of an unsuitable material for the high-load application. By replacing the washers with a thicker, more durable material, the plant significantly extended the lifespan of its gearboxes.
-
Story 2: A wind turbine manufacturer encountered excessive wear on thrust washers in its generators. Investigation showed that the washers had insufficient axial clearance. By adjusting the clearance, the wear problem was resolved, improving the performance and reliability of the generators.
-
Story 3: An aerospace contractor faced binding and seizing issues with thrust washers in its flight control systems. The washers were made of a material with a high coefficient of friction. By switching to a low-friction material, the contractor eliminated the binding and improved the safety and responsiveness of its flight control systems.
Call to Action
For optimal performance and reliability of your mechanical systems, carefully consider the selection and design of thrust washers. Contact a reputable supplier or consult with an experienced engineer for expert guidance and recommendations.