The Comprehensive Guide to Slotted Head Screws
In the realm of fasteners, the slotted head screw stands tall as a versatile and ubiquitous workhorse. From household repairs to industrial applications, this iconic screw has earned its place in every toolbox.
Anatomy of a Slotted Head Screw
The slotted head screw, also known as the straight-slot screw, comprises several key components:
-
Head: The flat, slotted surface that accepts a screwdriver for driving.
-
Slot: The linear indentation in the head that aligns with the screwdriver.
-
Shaft: The cylindrical portion of the screw that extends downwards from the head.
-
Threads: Helical grooves cut into the shaft that create a strong, interlocking connection with the mating surface.
-
Point: The sharpened tip of the screw that facilitates easy insertion into the material.
Applications of Slotted Head Screws
Slotted head screws are widely used in a range of applications, including:

-
Woodworking: Joining wood components, such as in furniture, cabinetry, and framing.
-
Metalworking: Securing metal components in electrical, plumbing, and automotive projects.
-
Electronics: Fastening circuit boards and electronic components.
-
Plastic: Joining plastic parts in appliances, toys, and consumer products.
Types of Slotted Head Screws
Slotted head screws come in various types to suit different needs:
-
Phillips Head: The most common type, with two cruciform slots for a Phillips screwdriver.
-
Pozidriv Head: An improved version of the Phillips head with four slots that provide increased driving torque.
-
Flat Head: A shallow head that sits flush with the surface of the material.
-
Round Head: A dome-shaped head that offers a more finished appearance.
-
Oval Head: An oval-shaped head that provides increased bearing surface and grip.
Sizes and Materials
Slotted head screws are available in a wide range of sizes, measured by their diameter (length of the screw) and thread count (number of threads per inch). Common diameters include #6, #8, #10, and #12, while thread counts vary based on the application.
They are typically made from steel, stainless steel, or brass, each offering different properties for specific requirements. Steel screws are strong and durable, stainless steel screws resist corrosion, and brass screws provide excellent electrical conductivity.

Installation and Removal
Installing and removing slotted head screws is a straightforward process:
Installation:

- Align the screwdriver with the slot in the screw head.
- Apply downward pressure while turning the screwdriver clockwise to drive the screw into the material.
- Continue driving the screw until it is fully seated.
Removal:
- Insert the screwdriver into the slot and apply downward pressure.
- Turn the screwdriver counterclockwise to loosen the screw.
- Once the screw is loose, remove it by hand or with pliers.
Drive Types
Slotted head screws can be driven with various drive types:
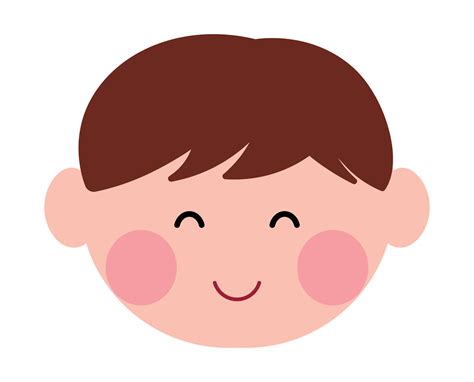
-
Manual Screwdriver: A traditional tool that requires manual effort to turn the screw.
-
Electric Screwdriver: A power tool that drives screws automatically, saving time and effort.
-
Impact Driver: A heavy-duty tool that delivers high torque for driving screws into hard materials.
Advantages and Disadvantages
Slotted head screws offer several advantages:
-
Simple and cost-effective: They are easy to use and relatively inexpensive to manufacture.
-
Versatility: They can be used in a wide range of applications and with various materials.
-
Durability: They provide a strong and secure connection.
However, slotted head screws also have some disadvantages:
-
Limited driving torque: Compared to other drive types, slotted screws can strip more easily when subjected to high torque.
-
Precision: They are more prone to cam-out, where the screwdriver slips out of the slot, especially when applying high torque.
-
Aesthetics: The visible slot may detract from the overall appearance of the project.
Alternatives to Slotted Head Screws
In certain applications, other screw types may provide advantages over slotted head screws:
-
Torx Head Screws: Offer higher driving torque and reduced cam-out.
-
Hex Head Screws: Provide a secure connection even under high loads.
-
Button Head Screws: Countersunk head that sits below the surface for a clean finish.
-
Socket Head Screws: Allow for easy installation and removal using a hex key or Allen wrench.
Stories and Lessons Learned
Story 1:
A carpenter was installing a new door frame in a house. He used slotted head screws to secure the frame to the wall. However, he overtightened one of the screws, causing it to strip. The frame became loose and unstable.
Lesson Learned: Avoid overtightening slotted head screws. Use the appropriate screwdriver and apply appropriate torque.
Story 2:
An electrician was wiring a circuit board. He tried to use a slotted head screwdriver to tighten a screw, but the screwdriver kept slipping out of the slot. He realized that the screw was a Phillips head and required a Phillips screwdriver.
Lesson Learned: Use the correct screwdriver for the screw head type to prevent cam-out.
Story 3:
A homeowner was attaching a metal bracket to a wall. He used slotted head screws made of steel. However, the screws quickly rusted due to exposure to moisture.
Lesson Learned: Choose the right material for the screw based on the environment and application. Stainless steel screws would have been a better choice in this case.
Effective Strategies for Using Slotted Head Screws
-
Use the right screwdriver: Ensure that the screwdriver matches the slot size and drive type of the screw.
-
Lubricate the screw: Applying a small amount of lubricant to the screw can reduce friction and prevent cam-out.
-
Start with a pilot hole: Pre-drilling a pilot hole slightly smaller than the screw diameter can make it easier to insert and drive the screw.
-
Drive the screw straight: Apply pressure perpendicular to the surface to avoid bending or breaking the screw.
-
Tighten gradually: Avoid overtightening the screw by turning it slowly and feeling for resistance.
Tips and Tricks
-
Use a magnetic screwdriver: A magnetic screwdriver can hold the screw in place for easier installation.
-
Drill a countersink: Drilling a small countersink around the screw head can allow it to sit flush with the surface.
-
Use a screw extractor: If a screw becomes stripped or damaged, a screw extractor can help remove it.
Common Mistakes to Avoid
-
Using the wrong screwdriver: Using a mismatched screwdriver can damage the screw head and make it difficult to remove.
-
Overtightening: Excessive torque can strip the screw head or break the screw.
-
Undertightening: A loose screw can lead to vibration, noise, or even failure of the joint.
-
Using the wrong material: Screws made of inappropriate materials may corrode, rust, or fail under loading.
-
Driving the screw at an angle: This can cause the screw to bend or break, leading to joint failure.
Conclusion
Slotted head screws are a versatile and widely used fastener with numerous applications across different industries. Understanding their anatomy, types, materials, and installation techniques is essential for successful and secure installations. By following the strategies and tips outlined in this guide, you can effectively utilize slotted head screws to achieve strong and reliable connections in your projects.