Replacing Screws with Threaded Inserts: A Comprehensive Guide
Introduction
In many engineering applications, it is often necessary to securely fasten components together. While screws have long been the go-to option for this purpose, threaded inserts have emerged as a highly effective alternative. This guide will provide a comprehensive overview of the advantages and processes involved in replacing screws with threaded inserts, offering valuable insights and guidance to enhance your design and assembly practices.
Advantages of Threaded Inserts
-
Improved Load Capacity: Threaded inserts distribute loads evenly over a larger surface area compared to screws, resulting in significantly higher load-bearing capacity. This is particularly beneficial in applications where high-strength joints are crucial.
-
Reduced Stress Concentration: Unlike screws, threaded inserts eliminate stress concentrations at the point of contact, reducing the risk of component failure due to fatigue or over-tightening.
-
Enhanced Durability: Threaded inserts are typically made of high-strength materials such as steel or stainless steel, offering excellent resistance to wear and corrosion. This ensures long-lasting performance, even in demanding environments.
-
Reusability: Threaded inserts can be easily removed and reinstalled multiple times without compromising their integrity. This makes them ideal for applications where disassembly and reassembly are frequently required.
-
Customization Options: Threaded inserts come in a wide range of sizes, shapes, and materials, allowing for customization to meet specific application requirements.
Types of Threaded Inserts

There are numerous types of threaded inserts available, each designed for different applications. Some of the most common types include:
-
Solid Threaded Inserts: These inserts provide a strong and reliable connection by creating a permanent thread in the host material.
-
Wire Threaded Inserts: Also known as coil inserts, these inserts are wound from a coil of wire and offer high elasticity for applications where there is limited space or access.
-
Keensert Threaded Inserts: These inserts feature a unique locking mechanism that prevents them from loosening, making them ideal for high-vibration environments.
-
Flexsert Threaded Inserts: These inserts are designed to accommodate misalignment and provide a secure connection even in applications with loose tolerances.
Process of Replacing Screws with Threaded Inserts
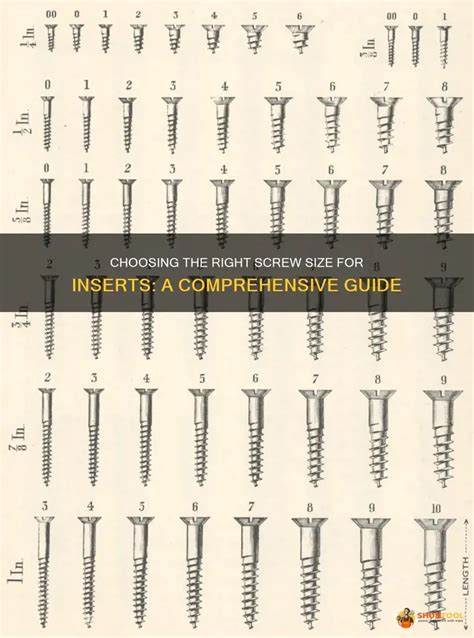
The process of replacing screws with threaded inserts involves the following steps:
-
Select the appropriate threaded insert: Determine the type, size, and material of insert that meets the application requirements.
-
Prepare the host material: Drill a hole with the specified diameter and depth for the insert. Ensure the hole is free of debris and burrs.
-
Install the threaded insert: Insert the threaded insert into the hole and tighten it using the recommended torque.
-
Countersink (optional): For a flush or below-surface installation, countersink the insert to the desired depth.
-
Tighten the bolt or screw: Thread the bolt or screw into the inserted thread and tighten to the specified torque.
Applications of Threaded Inserts
Threaded inserts are widely used in various industries and applications, including:
- Automotive: Engine components, suspension systems, and body panels
- Aerospace: Aircraft structures, landing gear, and engine mounts
- Electronics: Printed circuit boards, connectors, and chassis
- Manufacturing: Heavy machinery, production lines, and tooling
- Medical: Surgical implants, prosthetics, and medical devices
Stories and Lessons Learned
-
Increased Safety in Automotive Applications: A leading automaker replaced screws with threaded inserts in critical engine components, resulting in a significant reduction in vibration and noise while enhancing safety and reliability.
-
Improved Durability in Aerospace Equipment: An aerospace contractor utilized threaded inserts in landing gear systems, resulting in increased load capacity and wear resistance, extending the lifespan of the components.
-
Enhanced Performance in Electronics: By switching from screws to threaded inserts in printed circuit boards, a technology company achieved higher signal integrity and reduced component failure rates in high-frequency circuits.
Strategies for Effective Implementation
-
Consider load capacity and stress distribution: Carefully assess the load requirements of the application and select threaded inserts that can handle the anticipated loads.
-
Choose the right material: Select the material of the threaded inserts based on the environmental conditions and compatibility with the host material.
-
Proper installation techniques: Ensure proper installation of the inserts by following the manufacturer's instructions and using the recommended tooling.
-
Quality control: Establish rigorous quality control measures to verify the integrity of the connections and prevent premature failures.
-
Cost-benefit analysis: Evaluate the cost-benefit implications of using threaded inserts compared to screws to determine the most cost-effective solution.
Frequently Asked Questions (FAQs)
1. What is the typical cost of threaded inserts?
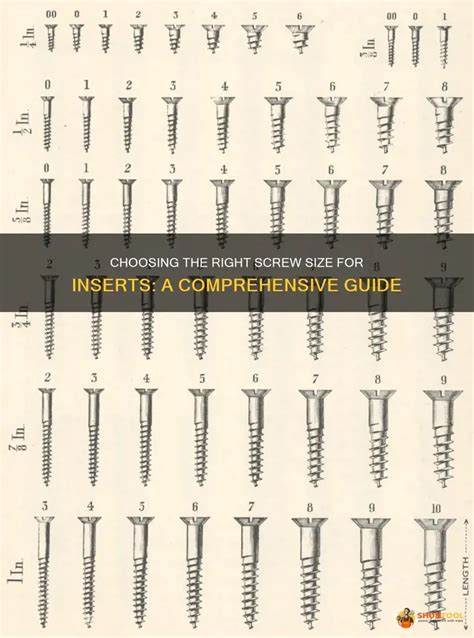
The cost of threaded inserts varies depending on the type, size, material, and quantity purchased. Contact manufacturers or distributors for specific pricing.
2. How can threaded inserts prevent thread damage?
Threaded inserts provide a sacrificial thread surface that absorbs wear and tear, preventing damage to the host material's threads.
3. Are threaded inserts suitable for use in blind holes?
Certain types of threaded inserts, such as self-tapping inserts, can be installed in blind holes without the need for pre-tapping.
4. How do I choose the correct threaded insert for my application?
Consider the load capacity, material compatibility, environmental conditions, and installation method. Consult with manufacturers or engineers for recommendations.
5. How can I prevent over-tightening of threaded inserts?
Use a torque wrench or other calibrated tool to tighten the inserts to the specified torque to avoid over-tightening and potential damage.
6. Are threaded inserts resistant to corrosion?
Some threaded inserts are made of corrosion-resistant materials, such as stainless steel, making them suitable for use in harsh environments.
Call to Action
If you are looking to enhance the strength, durability, and reliability of your assemblies, consider replacing screws with threaded inserts. Thoroughly evaluate the application requirements, select the appropriate threaded inserts, and follow proper installation techniques to reap the numerous benefits they offer. By embracing this innovative solution, you can optimize your designs and achieve better outcomes in various industries and applications.