The Ultimate Guide to Lathe Tools: Types, Applications, and Essential Techniques
Lathe tools, the unsung heroes of metalworking, play a crucial role in shaping and finishing various metal components. With their ability to remove material, create precise geometries, and generate smooth surfaces, these tools are indispensable in machine shops and manufacturing facilities.
In this comprehensive guide, we delve into the world of lathe tools, exploring their types, applications, and essential operating techniques. We provide valuable insights into the importance of choosing the right tool for the job and demonstrate how to maximize its efficiency and accuracy. Additionally, we highlight safety considerations, maintenance practices, and troubleshooting tips, ensuring that your lathe tooling knowledge is complete.
So, whether you are a novice machinist or a seasoned professional, this guide will equip you with the knowledge and skills you need to master the art of lathe tool operation.
Types of Lathe Tools
The vast array of lathe tools can be categorized into several primary types, each designed for specific operations and materials:

1. Cutting Tools
-
Turning Tools: Used for turning (reducing the diameter) and facing (creating a flat surface perpendicular to the axis of rotation) operations. They come in various shapes, including round, square, and diamond.
-
Boring Tools: Designed for enlarging existing holes or creating new ones. They have a bar-like structure with a cutting edge at the tip.
-
Grooving Tools: Used for cutting grooves or channels into the workpiece. They feature a narrow cutting edge and can come in different shapes and sizes.
-
Threading Tools: Specifically designed for cutting external and internal threads on the workpiece. They have a specific geometry that allows for precise thread creation.
-
Knurling Tools: Used to create a textured surface on the workpiece, improving grip or providing a decorative finish. They have a serrated cutting edge that imprints the desired pattern.
2. Non-Cutting Tools
-
Centering Tools: Used to center the workpiece accurately on the lathe. They come in different types, including live centers, dead centers, and rotating centers.
-
Steady Rests: Support and stabilize long or slender workpieces during machining operations. They prevent deflection and ensure precision.
-
Follow Rests: Similar to steady rests, but they move along the workpiece as it is being machined, providing continuous support.
-
Tool Holders: Secure and position lathe tools in the machine. They come in various types and sizes, depending on the tool and lathe model.
3. Measuring and Inspection Tools
-
Calipers: Used for measuring the dimensions, diameters, and depths of workpieces. They come in different types, including vernier, dial, and digital calipers.
-
Micrometers: Provide precise measurements of small dimensions and tolerances. They have a spindle and anvil that can be finely adjusted.
-
Dial Gauges: Used for measuring small displacements, deviations, or errors in workpiece dimensions. They feature a movable indicator that displays the measurement on a dial.
Applications of Lathe Tools
Lathe tools find application in a wide range of industries and tasks, including:
- Machining metal components for automotive, aerospace, and medical industries
- Creating custom parts and prototypes
- Repairing and restoring machinery and equipment
- Polishing and finishing metal surfaces
- Educational and research institutions
Essential Techniques for Lathe Tool Operation
Operating lathe tools requires knowledge, skill, and adherence to safety guidelines. Here are some essential techniques to master:

1. Tool Selection and Setup
- Choose the appropriate tool type, size, and material based on the operation and workpiece material.
- Secure the tool firmly in the tool holder to ensure stability and prevent slippage.
- Adjust the tool's cutting edge to the correct height and angle relative to the workpiece.
2. Speed and Feed Control
- Set the lathe spindle speed and tool feed rate according to the material being machined, tool type, and desired finish.
- Use higher speeds for softer materials and lower speeds for harder materials.
- Adjust the feed rate to control the amount of material removed with each pass of the tool.
3. Safety Precautions
- Wear appropriate safety gear, including safety glasses, gloves, and protective clothing.
- Ensure the lathe is properly guarded and that guards are in place before operating.
- Avoid touching the rotating workpiece or tool while the machine is running.
- Keep the work area clean and free of debris.
Why Lathe Tool Matters
The choice of the right lathe tool is crucial for achieving optimal machining results and ensuring workpiece accuracy, surface finish, and tool life. Consider these reasons why lathe tool matters:
-
Precision and Accuracy: Proper tool selection and setup allow for precise and accurate material removal, resulting in the desired workpiece dimensions and geometries.
-
Surface Finish: The sharpness and geometry of the cutting edge determine the surface finish of the workpiece, affecting its aesthetic appeal and functional performance.
-
Tool Life: Selecting the right tool material and operating parameters can significantly extend tool life, reducing downtime and maintenance costs.
-
Safety: Using the correct tool for the job minimizes the risk of accidents and injuries.
-
Efficiency and Productivity: Choosing the right tool and operating techniques can improve machining efficiency and increase productivity.
Benefits of Proper Lathe Tool Selection
Choosing the right lathe tool for the specific application provides numerous benefits:
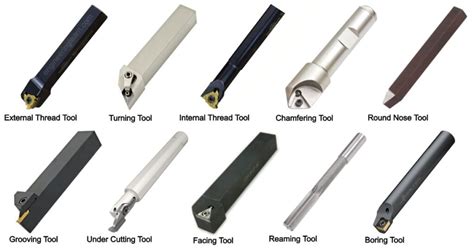
-
Reduced Machining Time: The proper tool allows for faster material removal and shorter machining cycles.
-
Improved Surface Finish: A sharp and appropriate tool produces a smoother and more consistent surface finish.
-
Extended Tool Life: Using the correct tool material and operating parameters minimizes wear and tear on the tool, extending its lifespan.
-
Energy Efficiency: Optimized tool selection can reduce energy consumption during machining operations.
-
Cost Savings: The combination of reduced machining time, extended tool life, and improved surface finish leads to significant cost savings.
Using Lathe Tools: Stories and Lessons Learned
To illustrate the importance of proper lathe tool selection and operation, let's explore three stories and the lessons they offer:
Story 1: The Wrong Tool for the Job
A machinist attempted to use a HSS (high-speed steel) lathe tool to machine a titanium workpiece. However, HSS is not suitable for titanium, resulting in rapid tool wear and poor surface finish. The machinist was forced to replace the tool with a carbide insert, which was better suited for the material, leading to improved results.
Lesson Learned: Choosing the right tool material is crucial for proper machining and efficient operation.

Story 2: Overfeeding the Tool
In a rush to complete a job, a machinist increased the feed rate of the lathe tool excessively. This caused the tool to chatter and break, resulting in a damaged workpiece and wasted time. By adjusting the feed rate to a more appropriate level, the machinist prevented tool breakage and achieved the desired surface finish.
Lesson Learned: Adjusting the feed rate according to the material and tool type is essential for optimal machining and tool preservation.
Story 3: Ignoring Safety Precautions
A machinist failed to wear proper safety glasses while operating a lathe. A metal chip flew off the workpiece and struck their eye, causing injury. By adhering to safety guidelines and wearing appropriate personal protective equipment, the machinist could have prevented the accident.
Lesson Learned: Safety precautions should never be ignored to avoid accidents and protect personal well-being.
Tips and Tricks for Lathe Tool Operation
Enhance your lathe tool operation skills with these helpful tips and tricks:
-
Use a sharp tool: A sharp cutting edge ensures cleaner cuts, better surface finish, and increased tool life.
-
Lubricate the tool: Applying cutting fluid or lubricant reduces friction, improves chip evacuation, and extends tool life.
-
Cool the workpiece: Overheating can cause distortion and affect machining accuracy. Use coolants or water jets to keep the workpiece temperature under control.
-
Maintain the toolholder: Clean and lubricate the toolholder regularly to prevent excessive wear and ensure smooth tool movement.
-
Check for tool chatter: Tool chatter can lead to poor surface finish and reduced accuracy. Adjust the tool setup or reduce the feed rate to eliminate chatter.
Frequently Asked Questions (FAQs)
1. What is the most important factor to consider when selecting a lathe tool?
The most important factor to consider is the material being machined. Different tool materials are suitable for different materials, such as HSS for softer materials and carbide inserts for harder materials.
2. How do I determine the correct speed and feed rate for a lathe tool?
Spindle speed and feed rate vary depending on the tool type, workpiece material, and desired surface finish. Consult the manufacturer's recommendations or refer to industry standards.
3. What are some common mistakes to avoid when using lathe tools?
Common mistakes include using a dull tool, overfeeding the tool, ignoring safety precautions, and failing to lubricate the tool.
4. How can I extend the life of my lathe tools?
Extend tool life by choosing the right tool material, operating the tool at appropriate speeds and feeds, lubricating the tool, and storing it properly.
5. What are some safety precautions to follow when operating lathe tools?
Wear appropriate safety gear, ensure the lathe is properly guarded, avoid touching the workpiece or tool while it is running, and keep the work area clean.
6. What are the key differences between different types of lathe tools?
Different types of lathe tools have specific designs for different operations, such as turning, boring, grooving, threading, and knurling.
Conclusion
Lathe tools are the cornerstone of metalworking, enabling the creation of precise and complex components. By understanding the types, applications, and essential techniques