Mastering Air Compressor Technologies: A Comprehensive Guide to Efficiency and Productivity
Air compressors are ubiquitous in modern industries, providing the vital force behind countless applications. From powering pneumatic tools to driving manufacturing processes, these machines play a crucial role in optimizing productivity and efficiency. In this comprehensive guide, we will delve into the intricacies of air compressor technologies, exploring their essential components, key principles, and practical applications.
Understanding Air Compressors: Foundation and Function
An air compressor is a remarkable device engineered to increase the pressure of air or other gases. Through a captivating process, it harnesses mechanical energy to reduce the volume of air, thereby heightening its pressure. This compressed air then becomes the driving force for a myriad of industrial and household applications.
Key Components of an Air Compressor
To fully grasp the mechanics of an air compressor, it is essential to understand its core components:
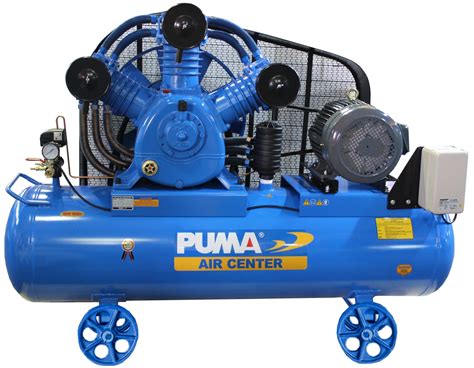
-
Compressor Element: The heart of the compressor, responsible for reducing air volume and generating pressure.
-
Reservoir/Tank: A storage vessel that stores the compressed air, maintaining a steady supply to downstream applications.
-
Motor: The driving force, providing the necessary mechanical energy to power the compressor element.
-
Controls and Instrumentation: Essential for monitoring and regulating the compressor's performance, ensuring reliability and safety.
Compression Principles: A Deeper Dive
The magic behind an air compressor lies in the compression principles it employs. Two prevalent methods dominate the industry:

-
Positive Displacement Compressors: These compressors physically reduce air volume by employing a rotating screw or reciprocating piston, directly increasing pressure.
-
Dynamic Compressors: Utilizing centrifugal or axial impellers, these compressors accelerate air, converting kinetic energy into pressure through aerodynamic forces.
Types of Air Compressors: A Tailored Approach
The diverse range of available air compressors reflects the varied demands of industries. Each type offers unique advantages, catering to specific applications:
-
Reciprocating Compressors: Ideal for low-volume, high-pressure tasks, these compressors feature a reciprocating piston within a cylinder.
-
Screw Compressors: Renowned for their efficiency and reliability, screw compressors employ a rotating screw mechanism for continuous compression.
-
Centrifugal Compressors: Designed for large-scale, high-volume applications, centrifugal compressors accelerate air through impellers.
-
Axial Compressors: Particularly effective for high-pressure applications, axial compressors utilize multiple rows of rotating blades to gradually increase pressure.
Selecting the Right Air Compressor: A Strategic Choice
Choosing the optimal air compressor requires careful consideration of factors such as:
-
Capacity (CFM): Indicates the volume of air delivered per minute, crucial for meeting application demands.
-
Pressure (PSI): Represents the maximum pressure the compressor can generate, essential for powering specific pneumatic tools.
-
Duty Cycle: Defines the percentage of time the compressor can operate at full load without overheating.
-
Energy Efficiency: A critical metric, directly impacting operating costs and environmental impact.
Applications of Air Compressors: A Tapestry of Industries
Air compressors find boundless applications across various sectors, including:

-
Manufacturing: Powering pneumatic tools, robots, and assembly lines.
-
Construction: Driving nail guns, sandblasters, and concrete breakers.
-
Automotive: Operating air-powered wrenches, lifts, and spray guns.
-
Healthcare: Assisting in surgical instruments, anesthesia machines, and X-ray equipment.
-
Household: Inflating tires, powering paint sprayers, and cleaning appliances.
Benefits of Air Compressors: Unleashing Productivity
The adoption of air compressors offers a multitude of advantages for businesses and individuals alike:
-
Increased Productivity: Powering pneumatic tools with greater efficiency, reducing labor requirements and expediting tasks.
-
Reduced Costs: Lower energy consumption, reduced maintenance expenses, and enhanced tool longevity contribute to significant cost savings.
-
Improved Safety: Pneumatic tools eliminate electrical hazards, reducing the risk of accidents in hazardous environments.
-
Versatility and Portability: Wide range of applications and portable options enable flexibility and maneuverability in various settings.
Effective Strategies for Efficient Air Compressor Operation
To maximize the performance and lifespan of an air compressor, implementing effective strategies is paramount:
-
Regular Maintenance: Adhering to a proactive maintenance schedule, including oil changes, filter replacements, and inspections, ensures optimal operation.
-
Proper Sizing: Choosing an air compressor with the appropriate capacity and duty cycle for specific applications prevents overloading and premature failure.
-
Efficient Air System: Minimizing leaks, optimizing air flow, and maximizing system pressure contribute to greater efficiency and energy savings.
-
Monitoring and Control: Employing sensors and control systems allows for real-time monitoring, adjusting performance parameters, and optimizing energy usage.
A Step-by-Step Approach to Troubleshooting Air Compressors
Addressing air compressor issues promptly and effectively is essential for maintaining productivity and minimizing downtime. Follow these steps for successful troubleshooting:
-
Identify the Problem: Observe symptoms, listen for unusual noises, and examine performance data to pinpoint the problem accurately.
-
Check Basic Components: Inspect air filters, oil levels, belts, and connections for any issues that may be causing the problem.
-
Examine Compressor Element: Evaluate the condition of the compressor element, including valves, pistons, or screws, for signs of wear, damage, or blockages.
-
Check Electrical Components: Verify the functionality of motors, switches, and control circuits using multimeters or other diagnostic tools.
-
Isolate the Problem: Use a process of elimination to identify the specific component or system causing the issue.
-
Fix and Test: Once the problem is identified, perform the necessary repairs or replacements and thoroughly test the compressor to ensure proper operation.
Why Air Compressor Maintenance Matters: A Path to Longevity
Regular maintenance is the cornerstone of ensuring air compressor reliability, performance, and longevity. Neglecting maintenance can lead to a cascade of problems:
-
Increased Downtime: Unattended issues can culminate in major breakdowns, resulting in costly downtime and production delays.
-
Reduced Efficiency: Clogged filters and worn components hinder compressor performance, leading to higher energy consumption and diminished output.
-
Safety Hazards: Overheating, leaking components, and electrical issues pose significant safety risks if maintenance is neglected.
-
Premature Failure: Lack of proper maintenance accelerates the degradation of compressor components, reducing its lifespan and ultimately requiring costly replacements.
Benefits of Regular Air Compressor Maintenance: A Smart Investment
Investing in regular air compressor maintenance yields a multitude of benefits that far outweigh the costs:
-
Extended Lifespan: A well-maintained compressor enjoys a significantly longer lifespan, maximizing its value and return on investment.
-
Optimal Performance: Regular maintenance ensures the compressor operates at peak efficiency, delivering consistent performance and meeting application requirements.
-
Reduced Operating Costs: By preventing breakdowns and premature failures, maintenance minimizes downtime, repair expenses, and energy consumption.
-
Improved Safety: Regular inspections and servicing mitigate potential safety hazards, creating a safer work environment.
Frequently Asked Questions (FAQs) about Air Compressors: Unlocking Common Concerns
To assist you further, here are answers to some frequently asked questions about air compressors:

Q: How often should I service my air compressor?
A: The recommended service interval varies depending on usage, but generally, annual maintenance is advisable for optimal performance and longevity.
Q: What are the signs of a failing air compressor?
A: Reduced output, excessive noise, overheating, and persistent leaks are common indicators of a failing air compressor.
Q: Can I perform air compressor maintenance myself?
A: Basic maintenance tasks, such as filter replacements and oil changes, can be performed by those with mechanical experience. However, complex repairs should be left to qualified technicians.
Q: How can I reduce the energy consumption of my air compressor?
A: Optimizing air system efficiency, using variable speed drives, and implementing energy-saving controls can significantly reduce energy consumption.
Q: What is the difference between a positive displacement and a dynamic compressor?
A: Positive displacement compressors directly increase pressure by reducing air volume, while dynamic compressors convert kinetic energy into pressure through aerodynamic forces.
Q: How do I choose the right air compressor for my application?
A: Consider factors such as capacity, pressure, duty cycle, and energy efficiency to select the optimal air compressor for your specific needs.
Conclusion: Embracing the Power of Air Compressors
Air compressors stand as indispensable tools for industries and households alike, powering countless applications and driving productivity. Understanding the fundamentals, types, and applications of air compressors enables informed decision-making and efficient operation. By implementing effective strategies and adhering to proactive maintenance, businesses and individuals can harness the full potential of these remarkable machines, ensuring reliability, reducing costs, and maximizing their return on investment.
Tables
Table 1: Air Compressor Types and Applications
Type |
Applications |
Reciprocating |
Low-volume, high-pressure tasks, air tools, medical equipment |
Screw |
Continuous compression, industrial applications, manufacturing |
Centrifugal |
Large-scale, high-volume applications, gas turbines, power plants |
Axial |
High-pressure applications, jet engines, gas compression |
Table 2: Benefits of Air Compressors
Benefit |
Explanation |
Increased Productivity |
Pneumatic tools reduce labor requirements and expedite tasks |
Reduced Costs |
Lower energy consumption, reduced maintenance expenses, enhanced tool longevity |
Improved Safety |
Pneumatic tools eliminate electrical hazards, reducing accident risks |
Versatility and Portability |
Wide range of applications and portable options enable flexibility |
Table 3: Air Compressor Maintenance Checklist
| **Task