Tubular Heaters: A Comprehensive Guide for Efficient Heating Solutions
Introduction
In the realm of heating, tubular heaters stand out as highly efficient and versatile solutions for a wide range of applications. These cylindrical heating elements, characterized by their hollow design and resistance wire coils, offer a plethora of advantages that make them an ideal choice for industrial, commercial, and residential settings.
Understanding Tubular Heaters
Construction:

Tubular heaters are meticulously crafted from high-grade metals, primarily stainless steel, incoloy, or copper. Their cylindrical shape houses resistance wire spirals strategically embedded in a dielectric material, such as magnesium oxide, which insulates and protects the heating element.
Operation:

When an electric current passes through the resistance wire coils, it generates heat, which is then transferred to the outer surface of the heater. Tubular heaters can operate on either single-phase or three-phase power, providing flexibility in electrical connections.
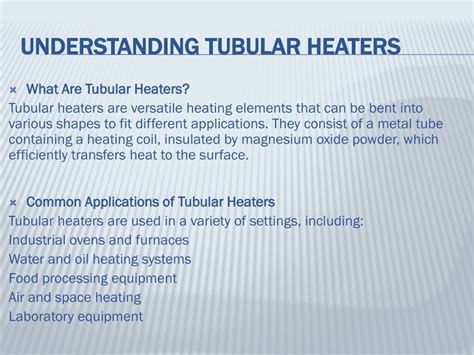
Applications:
The versatility of tubular heaters knows no bounds, making them suitable for a vast array of heating applications, including:
- Process heating
- Air heating
- Fluid heating
- Food processing
- Packaging
- Plastics molding
- Aerospace
Benefits of Tubular Heaters
Tubular heaters offer a myriad of benefits that contribute to their widespread use:
-
High Efficiency: Tubular heaters boast impressive heat transfer rates, ensuring maximum energy utilization and minimizing operating costs.
-
Compact and Durable: Their compact design makes them space-efficient, while their rugged construction ensures long-lasting performance in harsh industrial environments.
-
Corrosion-Resistance: Stainless steel and other metal alloys used in their construction provide excellent corrosion resistance, enabling their use in corrosive environments.
-
Customizable: Tubular heaters can be tailored to specific heating requirements, including temperature ranges, dimensions, and power ratings.
Types of Tubular Heaters
The diverse range of tubular heaters available meets the varying needs of different applications. Key types include:

-
Straight Tubular Heaters: The most common type, offering simplicity and versatility.
-
Bent Tubular Heaters: Designed for tight spaces and complex heating patterns.
-
Flanged Tubular Heaters: Feature flanges for easy mounting and heat transfer optimization.
-
Immersion Tubular Heaters: Submerged directly into fluids for heating applications in tanks, vessels, and pipelines.
Selecting the Right Tubular Heater
Choosing the appropriate tubular heater for a specific application is crucial. Key factors to consider include:
-
Heat Output: Determine the required heating capacity based on the desired temperature and the mass or volume of the material to be heated.
-
Dimensions: Ensure that the heater fits within the available space, including clearance for electrical connections and maintenance.
-
Materials: Select materials compatible with the operating environment and the substance being heated.
-
Mounting: Choose the appropriate mounting method, whether it be flange, bracket, or immersion.
Effective Strategies for Tubular Heater Use
Maximizing the performance and efficiency of tubular heaters involves employing effective strategies:
-
Proper Installation: Ensure proper mounting and electrical connections to prevent overheating and ensure optimal heat transfer.
-
Temperature Control: Use thermostats or temperature controllers to regulate the heater's temperature, preventing overheating and avoiding damage.
-
Regular Maintenance: Conduct periodic inspections and cleanings to remove dirt and debris, ensuring optimal heat transfer and prolonging the heater's lifespan.
Tips and Tricks for Tubular Heater Applications
-
Consider Heat Loss: Account for heat loss in the application to ensure the heater provides sufficient heat output.
-
Use Reflector Shields: Enhance heat transfer and reduce energy consumption by using reflector shields around the heater.
-
Avoid Oversizing: Select a heater with a capacity slightly higher than the required heat output to prevent overheating and premature failure.
Why Tubular Heaters Matter
Tubular heaters play a pivotal role in various industries and applications, contributing to:
-
Increased Productivity: Efficient heating processes accelerate production rates and output.
-
Improved Product Quality: Accurate and consistent heating ensures product quality and reduces defects.
-
Reduced Energy Consumption: High-efficiency tubular heaters minimize energy costs and contribute to environmental sustainability.
-
Enhanced Safety: Proper installation and maintenance of tubular heaters ensures a safe working environment free of fire or electrical hazards.
Pros and Cons of Tubular Heaters
Pros:
- High heat transfer efficiency
- Compact and durable construction
- Corrosion resistance
- Customizable to specific requirements
Cons:
- Initial cost can be higher than other heating options
- Require proper installation and maintenance
- Can generate electromagnetic fields (controlled by proper grounding)
Market Analysis
According to Grand View Research, the global tubular heater market is projected to reach USD 3.49 billion by 2027, growing at a CAGR of 4.3% during the forecast period. This growth is attributed to increasing industrial automation, rising demand for energy-efficient heating solutions, and the expansion of the food and beverage industry.
Leading Manufacturers
Key players in the tubular heater market include:
- Chromalox
- Watlow
- Omega Engineering
- Kanthal
- BEKAert
Technical Specifications and Safety Guidelines
Table 1: Typical Operating Temperatures of Tubular Heaters
Material |
Operating Temperature (°F) |
Stainless Steel |
1200-1800 |
Incoloy |
1800-2200 |
Copper |
500-1000 |
Table 2: Electrical Characteristics of Tubular Heaters
Voltage |
Power |
120 VAC |
100-1000 W |
240 VAC |
200-2000 W |
480 VAC |
400-4000 W |
Table 3: Safety Guidelines for Tubular Heater Installation
- Ground the heater properly to prevent electrical shocks.
- Ensure adequate ventilation around the heater to prevent overheating.
- Keep flammable materials away from the heater.
- Wire the heater according to the manufacturer's instructions.
- Regularly inspect the heater for any damage or loose connections.
Conclusion
Tubular heaters are versatile and efficient heating solutions that offer numerous advantages in a wide range of applications. Their high heat transfer rates, compact design, and durability make them ideal for industrial, commercial, and residential settings. By following effective strategies, employing tips and tricks, and adhering to safety guidelines, tubular heaters can provide maximum performance, energy efficiency, and a safe working environment.